- By Softlink Global
- February 15, 2023
- General
We are entering a new era of the supply chain where humans and intelligent machines are collaborating to driving business results that have never been possible before. Before COVID-19, a vast majority of supply chain organizations felt that, they were capable of sensing and responding to disruptive events. But the new level of complexity introduced by the COVID-19 pandemic invalidated their capabilities and accelerated their investments in digital technology. A study found that in response to COVID-19, 47% of companies thought of redesigning their digitalization strategy and increasing the speed of their digital initiatives to find innovative ways to drive growth.
Many businesses introduced intelligent technology to reduce in-person interactions, and others completely reimagined their supply chain operations using technologies like AI, digital twins, the internet of things (IoT) and cloud computing. The result? A new level of visibility and speed fundamentally changed the companies started planning, sourcing, manufacturing, supplying and servicing with historic insight across the product and operating value chain.
So it is evident that the latest wave of digitalization will revolutionize the way the supply chain companies operate today. Thus supply chain companies that can effectively combine human ingenuity and automation will be positioned to achieve a competitive advantage.
Now the question is, what expertise will your next-generation supply chain managers require? Computer programming? Data analytics? Advanced robotics? Maybe all those and more.
According to McKinsey Global Institute research, more than half of the tasks carried out manually today will be automated by 2055.
This will automatically require process transformations and the implicit need to reskill and up skill the workforce.
But what is the current state of supply chain industry skills capabilities?
Currently, the supply chain workforce are not empowered enough to adopt new technologies, and effectively leverage data and analytics require for the new supply chain capabilities. We’ve known for some time that the quality of managing change or transformation program fail in supply chain by 70% due to the lack of necessary skills and capabilities to support in the effective sense and response capabilities.
To support the digital supply chain agility, the chief supply chain officers (CSCOs) need to identify and look toward reskilling and redeploying today’s workforce to achieve the required competencies. They need to train the people and upgrade their capabilities to support new and more digital workflows.
Learn more from our experts how you can digitalize your freight forwarding & logistics business.
Where is your supply chain workforce headed?
For employees to work digitally and support the efforts of becoming a digital business, the chief supply chain officers (CSCOs) will need to feature digital dexterity competencies. Digital dexterity can be defined as mind sets, beliefs and behaviour of the workforce that are ready to adapt the digital business transformation.
And with an increased focus on data and analytics in the supply chain, the average employee will need to develop skills in data literacy and the ability to work digitally.
Research shows the typical supply chain skills prevalent in most companies today will become obsolete sooner or later and won’t be able to compete with the increasing need for the digital supply chain in the future. More than 80% of supply chain leaders believe that their organization need to develop employees with boarded skills as they are working towards digitally transforming their supply chain. They will need a workforce that is more resilient during uncertain times, relevant to customers and employees, can solve complex, cross-industry problems and responsible toward the environment and society.
While this is a difficult proposition, trying to ensure that the future supply chain workforce has the right skills to make that transformation successful and digital dexterity together. But yet, this is achievable with the right strategy and people-first approach.
That’s why chief supply chain officers must act now to start building, hiring and up skilling the workforce with an ambition towards achieving changes they’ll need to make for the future. And as they do, they should consider the value they can derive by taking steps to help the employees to build new skills.
The path forward: Knowing where & how to start building skills for the future
One of the major challenges faced by supply chain companies today is identifying the specific skills they need to develop and grow competitive people capabilities. Without a clear road map and understanding of their employees’ current capabilities or their future skill requirements, supply chain organizations are working in the dark. So, many end up hiring external talents to fulfil the immediate skill gap.
Companies that have a clear perspective of what they need regarding talent depend on external talent pools but at the same time also take a strategic approach to build the skills of the existing workforce simultaneously.
Organizations that invest in developing their people and adapting an effective capability-building formula see a higher success rate while launching a transformational change program.
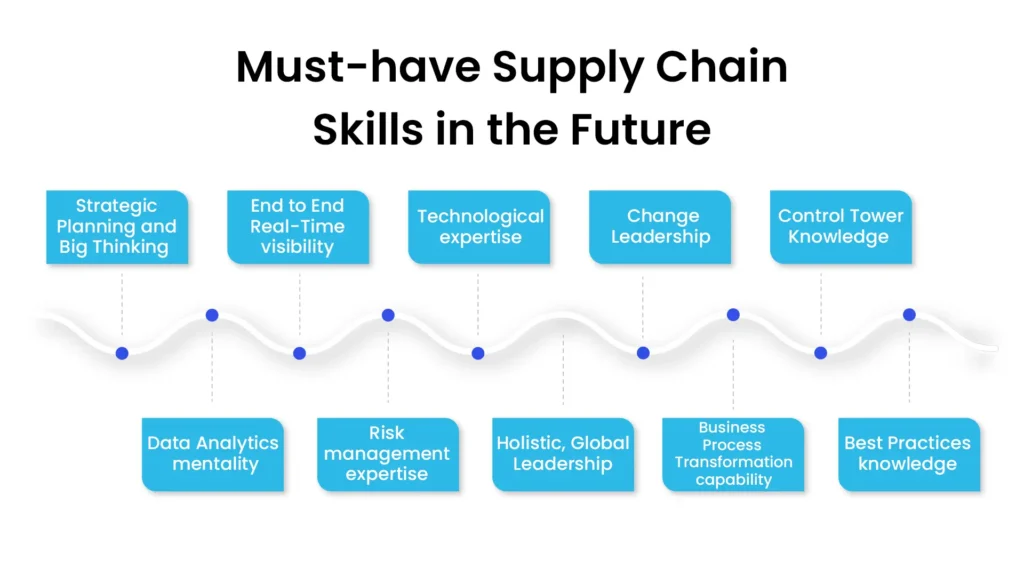
How to design a successful supply chain capability-building program?
A thoughtful approach to the design and deployment of capability building to the next generation of supply-chain operations starts with identifying the skill gaps and designing the capability program curriculum, implementation and sustainment with regular up skilling.
Identify skill gaps – Start with identifying the knowledge gap and the future requirements from the role of the existing workforce. Assess individual and collective skill levels against your business and supply-chain objectives. If the internal talent lack the required skills to serve the purpose, plan to hire talent pools from external sources.
Design the capability program curriculum – Prepare the design and scope of the capability-building program and learning journey. The curriculum should include both theory and as well as hands-on experimentation in realistic environments. Knowledge and the practical applications of future technologies like data analytics, cloud, Internet of Things, intelligent automation, and virtual and augmented reality in the supply chain can help broaden the perspective of today’s supply chain professionals.
Implement and sustain regular skilling up – Simply designing a well-articulated capability-building curriculum does not guarantee a successful up-skilling of the workforce. The program’s success also depends on the delivery mechanism, periodic workshops with subject-matter experts and industry partners, formal tracking and reporting mechanisms and measuring progress.
Build a new generation of workforce to transform your supply chain
Train for cross-functional capabilities – Currently, the supply chain ecosystem work on an interconnected model. Supply chain companies no longer have siloed functional teams handling a series of transactional elements that they connect at the end using some traditional method. Instead, CSCOs need to train and build workforce teams that can work for cross-functional operations. When people are given training with cross-functional capabilities, they have better understanding of the entire operations, can proactively solve problems using data and minimize the “data latency” challenge that plagues siloes decision-making.
Encourage employees to increase digital fluency –Digital fluency can be defined as the ability to discover, evaluate, and use information and technology effectively and ethically. Supply chain companies should start assessing and evaluating the digital fluency of their workforce. Companies should encourage employees to explore the latest technologies that can impact the current and future supply chain and be better prepared to use them effectively.
Digital fluency will enable them to build the technological foundations, help them unleash their creative side and decision-making capabilities, and build leaders from within the organization.
Rotating assignments to broaden horizons – Rotating the assignments at regular intervals among the various supply chain departments often help employees to gain a bigger and better perspective about the entire workflow mechanism. Understanding the collaboration and interdependency across functions will not only help their performance in their current roles but also, help them understand the whole network effectively. Setting up a shared approach and rotating assignments to broaden the horizon will send clear messages to everyone in the organization of the “continuous learning” culture.
There’s no doubt that in the coming years, the supply chain industry will see a vast digital transformation, so CSCOs should start preparing for the future supply chain workforce today. Building a powerful workforce to transform your supply chain will become more important to a company’s success than ever. The modern supply chain will require people with the mind set of transformation at their heart. So supply chain organizations that plan to embrace digital transformation, and more advanced technologies, must acknowledge that their workforce is what will set them apart from the competition. And they must make it a priority to prepare their employees for the future and emerge as an industry leader and a capability accelerator.